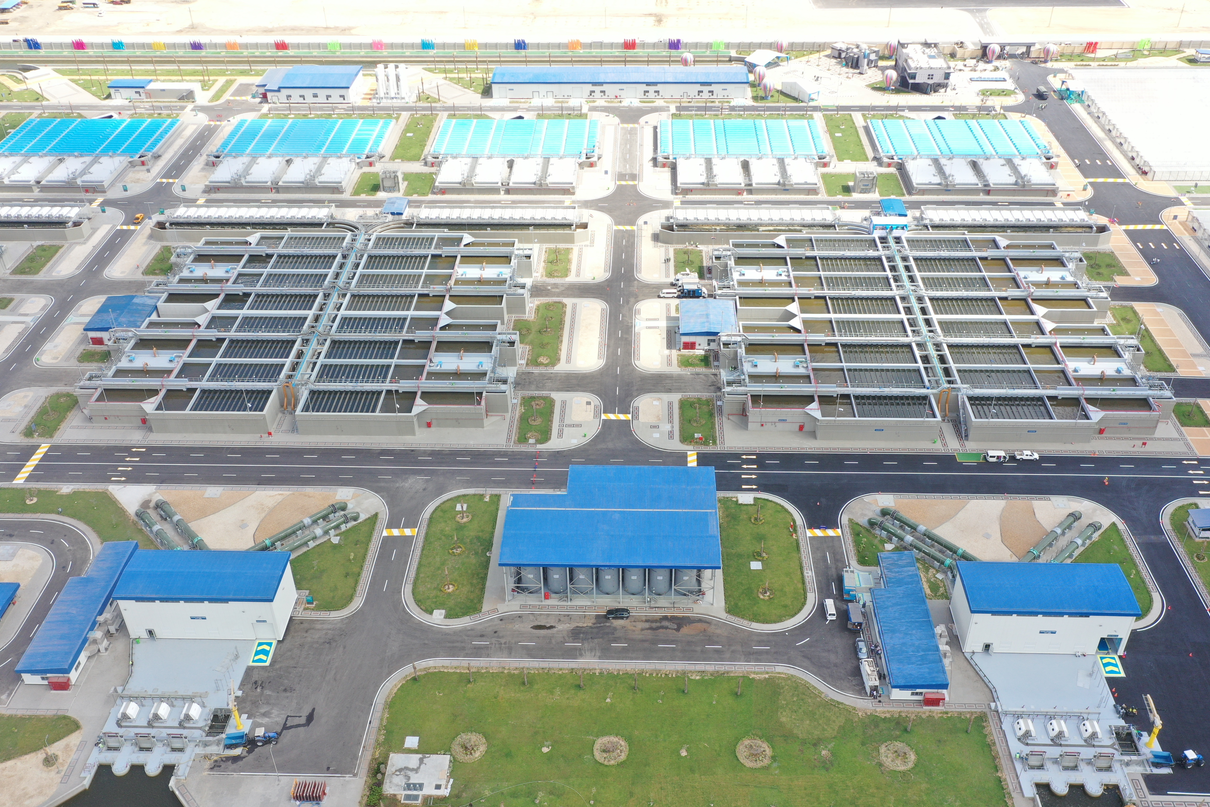
Uno de los proyectos más importantes para aprovechar los recursos naturales de Sinaí y promover su desarrollo
En la zona de Bahr Al-Baqar la única solución que existía para regar era con aguas residuales agrícolas, industriales y municipales, asumiendo los riesgos que eso conlleva para la salud.
Esto se debe a cómo era el bombeo y el riego de los cultivos locales, por eso era de urgencia realizar un proyecto donde se aplicasen y combinasen diversas técnicas de tratamiento como la coagulación, floculación, decantación, filtración y desinfección del agua. Así, además, se conseguiría recuperar y cultivar tierras agrícolas, mientras se fortalecían las economías locales y se mejoraría el nivel de vida de las personas.
Por eso, nos pusimos manos a la obra y construimos la planta de tratamiento de aguas más grande de África y una de las más grande del mundo, ubicada en el noroeste de Egipto, con capacidad de tratamiento de 5.6 millones m3/d, donde el agua tratada es utilizada para regar unas 140.000 hectáreas de tierras de cultivo, el equivalente a 280.000 campos de fútbol, a lo largo del Canal de Suez en Egipto.
La recién construida planta de tratamientos de aguas residuales de Bahr al-Baqar, se encuentra situada en el noroeste de Egipto, a 10 km sur de los túneles Port Said, una zona con el potencial suficiente como para causar ese impacto en la población y en las zonas de cultivo.
¿Cómo lo hicimos? Utilizando válvulas y tuberías de plástico en vez de metálicas.
A priori, puede parecer una solución descabellada, pero el plástico es un tipo de material que presenta mayor resistencia a la corrosión proveniente del tratamiento químico al que se somete el agua para hacerla apta para el regadío y tiene una mayor vida útil, por lo que supone un ahorro de costos asociados.
Desde el inicio del proyecto, ofrecimos el apoyo y la orientación técnica de nuestros expertos, poniendo a disposición, un equipo multidepartamental, compuesto por profesionales de la compañía de distintos países, que guiaron respecto a nuestra amplia cartera de productos en diferentes materiales termoplásticos para conducir con seguridad diferentes tipos de fluidos.
Seleccionamos meticulosamente los productos que mejor se ajustaban a los requerimientos de la planta: válvulas manuales y motorizadas de PVC-U, PP y PVDF, como alternativa a las válvulas metálicas.
Este reto sin precedentes supuso implantar una red de tuberías con:
- Más de 300 válvulas de plástico en PVC-U, PP y PVDF, incluidas las actuadas con posicionadores.
- Más de 4 kilómetros de tuberías con diámetros de entre 20 y 200 mm.
- Más de 7.600 accesorios para realizar conexiones con tuberías previamente instaladas.
Además, trabajamos en la logística, la fabricación de tuberías, accesorio y válvulas termoplásticas, y en el montaje de los actuadores para esas válvulas motorizadas. Todo desde diferentes países.
Y el éxito no se hizo esperar
La rapidez y eficiencia de Aliaxis fue clave en todo el proceso. Gracias a esta agilidad, pudimos adelantarnos a los plazos de entrega que se barajaban para los equipos y productos metálicos, lo que siempre es una ventaja a ojos del cliente.
Y por supuesto, este gran proyecto no hubiera sido posible sin el esfuerzo y la experiencia de los trabajadores de Aliaxis: Nuestra planta de fabricación en Casella y el equipo técnico español con sede en Madrid y Okondo.